„Wir müssen den Ölnebel aus der Halle entfernen und ich möchte damit keine Probleme haben.“ Das ist der Grund, warum Lucien Heemskerk von Heemskerk Fijnmechanica in Waddinxveen 3nine-Ölnebelabscheider in sieben seiner Maschinen eingebaut hat. Die Ölnebelabscheider, die in den Benelux-Ländern von der Firma Glavitech vertrieben werden, bieten nicht nur bessere Luftqualität in der Fabrik, sondern verringern auch die Temperatur in den Werkzeugmaschinen und den Kühltanks.
Heemskerk Fijnmechanica ist spezialisiert auf individuelles CNC-Fräsen und Drehen von qualitativ hochwertigen Produkten nach Kundenspezifikation. Das Familienunternehmen stellt außerdem Vakuumformen für Verpackungen von Lebensmitteln und anderen Produkten her. Heemskerk verfügt über einen umfassenden Maschinenpark mit ca. 50 CNC-Maschinen, von denen 13 über Roboterbeladung verfügen. Dies ermöglicht ihm, flexibel auf die individuellen Wünsche und Bedürfnisse ihrer Kunden einzugehen.
Regelmäßige Investition
Heemskerk investiert regelmäßig in Maschinen und Automatisierung. Im Jahr 2015 wurden acht Fünfachsenmaschinen installiert und dieses Jahr folgt eine neunte, alle sind mit einem Roboter ausgestattet. In der Fabrik gibt es 23 CADCAM-Stationen, auf die alle Mitarbeiter für Programmierungen zugreifen können. „All unsere Investitionen sind auf den Fortschritt ausgerichtet“, sagt Lucien Heemskerk. „Wir können somit effizienter arbeiten und Kosten reduzieren. Denn man muss realistisch sein: Maschinelle Bearbeitung ist ein extrem hart umkämpfter Markt, jetzt noch stärker als früher. Heutzutage ist Qualität von höchster Wichtigkeit, aber gleichzeitig wird der Preis der bestimmende Faktor.“
Gesundes Arbeitsumfeld
Investitionen in ein gesundes Arbeitsumfeld werden ebenfalls getätigt. Heemskerk möchte durch die Schaffung einer sicheren und gesundheitsfördernden Arbeitsumgebung ein erstklassiger Arbeitgeber sein und von den dadurch zu erzielenden Effizienzsteigerungen profitieren. Auf dem Dach der Fabrik befinden sich drei Klimaanlagen, die den ungesunden Ölnebel beseitigen, der während der Bearbeitungsprozesse in die Luft gelangt. Neue Werkzeugmaschinen werden immer mit einer Ölnebellösung gekauft. Heemskerk probierte im Laufe der Jahre verschiedene Arten von Ölnebellösungen aus, die alle Filtereinsätze oder elektrostatische Filter verwendeten. „Aber diese Filter sind störungsanfällig: sie verschmutzen, wodurch ihre Funktion beeinträchtigt wird, mal hat ein Ventilator eine Störung, mal bricht ein Kabel. Die Bediener reinigen die Ölrückstände auf den Maschinen nicht, sodass man immer Reinigungsfirmen beschäftigen muss. Am Ende muss man die Filter ersetzen. Kritisch betrachtet verfügen die [traditionellen] Systeme über einige gute Qualitäten, sind aber nicht vollkommen. Sie erfordern einen großen Wartungsaufwand und man hat oft Probleme mit ihnen. Die Wartungskosten summieren sich unbemerkt und sind am Ende ziemlich hoch.“
Abscheidung statt Filtern
Lucien Heemskerk hatte schon früher Interesse an den Ölnebelabscheidern des schwedischen Herstellers 3nine, jedoch schreckte ihn der Preis ab. Als er jedoch wieder mit einer riesigen Wolke an Ölnebel in der Fabrikhalle konfrontiert war, wurde ihm klar, dass er eine bessere Lösung braucht. Er kontaktierte Pieter Glavimans von Glavitech, dem 3nine-Vertriebspartner im Benelux-Raum, und bestellte sechs Ölnebelabscheider. Wie der Name schon sagt, filtern diese Geräte nicht sondern sie scheiden ab. Mit traditionellen mechanischen Technologien wird der Ölnebel in Filtermedien und den elektrostatischen Einheiten gesammelt. Dabei kommen mehrere Filterplatten zum Einsatz. Der innovative 3nine-Ölnebelabscheider jedoch trennt die flüssigen Partikel aus der Prozessluft und ermöglicht so eine Wiederverwendung der Kühlschmierstoffe. Er reinigt die Luft effektiv und hilft dabei, die Temperatur in den Werkzeugmaschinen konstant zu halten. Die 3nine-Ölnebelabscheider verwenden eine innovative Art der Tellerseparation, wodurch alle Partikel > 1μm zu 100% aus der Prozessluft abgeschieden werden. Alle Partikel < 1µm werden hauptsächlich durch die Tellerseparation sowie durch den zusätzlich nachgeschalteten HEPA-Filter zu 99,9% entfernt.
Diese Art der Abscheidung garantier minimale Wartung und minimalen Filterwechsel.
sagt Pieter Glavimans.
Für große Mengen an Ölnebel
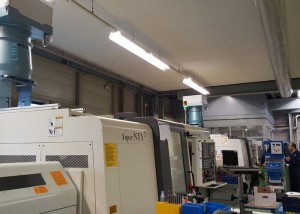
Heemskerk Fijnmechanica benutzt Lina 500 aus der 3nine-BLUE LINE-Serie. Hier sehen Sie ein Beispiel von zwei Linas, die auf Nakamura-Tome-Drehmaschinen installiert sind und rund um die Uhr laufen.
Heemskerk hat einige Werkzeugmaschinen in seinem Maschinenpark, die große Verschmutzung produzieren, wie z. B. die Drehmaschinen, die häufig mit Doppelwerkzeughaltern arbeiten. Für die Nakamura-Tome-Drehmaschinen, die im 24-Stundenbetrieb laufen, wurde die Lina 500 aus der 3nine-BLUE LINE-Serie gewählt. Die Ölnebelabscheider aus der BLUE LINE-Serie produzieren Luftströme von 500 m³/h bis zu 2500 m³/h und eignen sich für Kabinengrößen zwischen 5 m³ und 30 m³. Die Lina 500 ist das kleinste Modell. Sie wurde eigens für kleine, gekapselte Werkzeugmaschinen mit einem Kabinenvolumen von bis zu 5 m³ entwickelt und produziert einen Luftstrom von bis zu 500 m³/h. Die Ölnebelabscheider von 3nine können direkt auf die Maschine montiert werden und sparen so an Stellfläche und unnötiger Verrohrung.
Heemskerk Fijnmechanica erwarb ebenfalls einen Clara-Ölnebelabscheider, der mit zwei Fertigungszentren verbunden wurde. Die Clara eignet sich für Maschinen mit einer Kabinengröße von bis zu 10 m³. Alle 3nine-Abscheider sind mit dem automatischen Reinigungssystem CIP (Cleaning in Place) ausgestattet. Das CIP hält die Teller und Rotoren sauber, indem es sie regelmäßig mit sauberen Kühlmitteln aus der Maschine besprüht.
Dadurch erfordern die Abscheider kaum Wartung und man muss sich über Jahre hinweg keine Gedanken darüber machen. „Das ist, was ich will“.
sagt Heemskerk.
Weitere Vorteile
Die Ölnebelabscheider sind seit nahezu einem halben Jahr im Einsatz und obwohl Heemskerk und seine Mitarbeiter schon bemerkt haben, dass die Luft sauberer ist, wollte er es dennoch nachmessen. „Wir haben die Luft, die aus dem Ölnebelabscheider austritt, gemessen, und waren positiv überrascht. Wir konnten einen Wert von 0,004 mg/m³ sehen, während wir mit dem alten System 14 mg/m³ erreichten – das war wirklich nur ein Schornstein“.
Zusätzlich zu der sauberen Luft bieten die 3nine Ölnebelabscheider noch weitere Vorteile. Aufgrund des stärkeren Luftstroms und des hohen Abscheideniveaus wird die Hitze effektiv abgeführt. Die Temperatur in den Werkzeugmaschinen bleibt konstant, sogar im 24-Stunden-Betrieb. Eine konstante Temperatur der Werkzeugmaschinen ist ein enormer Vorteil wo Maß- und Wiederholgenauigkeit gefordert sind, da der softwarebasierte Temperaturausgleich der Maschinen nicht 100 % genau ist.
Durch die kühleren Schmierstoffe entstehen auch weitere Vorteile, vor allem für ihre Drehmaschinen mit mehreren Werkzeughaltern und Spindeln, die über mehrere Kühlpumpen verfügen und auf den gleichen Kühltank zugreifen. Dies führte in der Vergangenheit zu einem Temperaturanstieg im Kühltank, aber gemäß Heemskerks eigenen Messungen ist die Kühlmitteltemperatur dank des 3nine-Ölnebelabscheiders von 34 auf 24,4 Grad Celsius abgesunken. „Wir sprechen von einem durchschnittlichen Temperaturunterschied von 10 Grad“, sagt Heemskerk. „Niedrigere Temperaturen des Kühlmittels bedeuten weniger Instabilität, weniger Schaumbildung und weniger Bakterien-/Pilzinfektionen.“
Für ihn besteht kein Zweifel, dass noch mehr Ölnebelabscheider von 3nine installiert werden. „Sechs Systeme auf einmal zu installieren war eine große Investition für uns. Aber ab jetzt werden wir sie standardmäßig auf allen neuen Maschinen installieren, dann merkt man es nicht so. Zusätzlich zur sauberen Luft schafft der Ölnebelabscheider verlässlichere Arbeitsprozesse. Und das ist es, was wir wollen, vor allem für robotisierte 24-Stunden-Prozesse. Am Ende muss man aus Gesundheits- und Sicherheitssicht immer in eine Lösung zur Reinhaltung der Luft investieren. Die Wartungskosten für diese Geräte summieren sich jedoch und ab einem bestimmten Punkt müssen diese Kosten wieder aufgefangen werden. Wenn man etwas findet, das die Ausfallquote deutlich senkt, wird es möglich.“
Dieser Artikel ist frei aus dem Holländischen ins Deutsche übersetzt worden. Den Original-Artikel finden Sie hier.